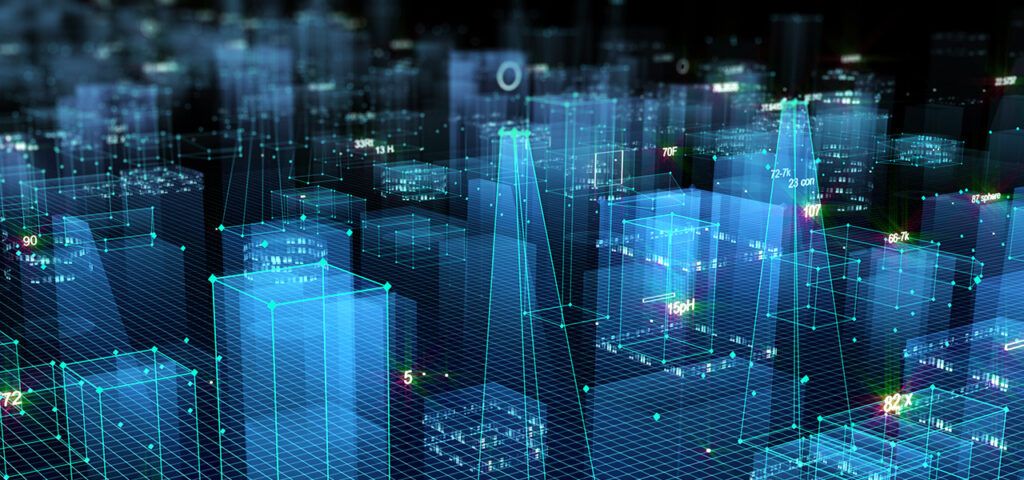
Sustainable and Resilient Smart Cities: Digital Twins - Revolutionizing Industry 4.0 and Beyond
Digital twin is a technology that is rapidly gaining traction in the world of Industry 4.0. It is a digital replica of a physical asset or system, such as a machine, a building, or a city. The digital twin is created by using data collected from sensors and other sources, and it is used to simulate the behavior and performance of the physical asset or system. This technology has the potential to revolutionize the way we design, build, and operate physical assets and systems, and it is already being used in a variety of industries, including manufacturing, construction, and healthcare.
One of the key benefits of digital twin technology is that it allows us to simulate and optimize the performance of physical assets and systems in a virtual environment, before they are built or deployed in the real world. This can help to reduce costs, improve efficiency, and minimize risks. For example, in the manufacturing industry, digital twin technology can be used to simulate the production process of a new product, and to identify and eliminate potential bottlenecks and inefficiencies before the product is actually manufactured. This can help to reduce the time and cost required to bring a new product to market.
Another benefit of digital twin technology is that it allows us to monitor and analyze the performance of physical assets and systems in real-time, using data collected from sensors and other sources. This can help to identify and diagnose problems before they become serious, and to optimize the performance of the asset or system over time. For example, in the healthcare industry, digital twin technology can be used to monitor the vital signs of patients in real-time, and to alert healthcare providers if there are any signs of a potential health problem. This can help to improve the quality of care and reduce the risk of complications.
Overall, digital twin technology is a game-changing technology that has the potential to transform the way we design, build, and operate physical assets and systems. It is already being used in a variety of industries, and its use is likely to become even more widespread in the coming years.
How Digital Twins Are Made: A Closer Look
Digital twins are virtual replicas of physical assets or systems, and they are created by using data collected from sensors and other sources. These virtual replicas can be used to simulate the behavior and performance of the physical asset or system, and can provide valuable insights into how it can be optimized and improved. In this blog post, we’ll take a closer look at how digital twins are made.
Step 1: Collecting Data
Real-Time Monitoring and Performance Analysis for Enhanced Outcomes
The first step in creating a digital twin is to collect data from sensors and other sources. This data can include information about the physical characteristics of the asset or system, such as its size, shape, and materials, as well as data about its performance, such as temperature, pressure, and vibration. This data is typically collected in real-time, using a variety of sensors and other monitoring devices.
Step 2: Creating a 3D Model
Optimizing Efficiency and Minimizing Risks through Virtual Simulation
Once the data has been collected, it is used to create a 3D model of the physical asset or system. This model is a virtual representation of the asset or system, and it includes all of the relevant physical characteristics and performance data. The 3D model can be created using a variety of software tools, such as computer-aided design (CAD) software or 3D scanning technology.
Step 3: Simulating Performance
Simulating the Future: Enhancing Performance through Digital Twins
Once the 3D model has been created, it is used to simulate the performance of the physical asset or system. This simulation can be used to identify potential problems or inefficiencies, and to test different scenarios and configurations. The simulation can be run in real-time, using data collected from sensors and other sources, and can provide valuable insights into how the asset or system can be optimized and improved.
Step 4: Integrating with Other Systems
Beyond the Virtual Realm: Integrating Digital Twins into Real Systems
Once the digital twin has been created, it can be integrated with other systems, such as control systems or data analytics platforms. This integration allows for real-time monitoring and analysis of the performance of the physical asset or system, and can provide valuable insights into how it can be optimized and improved over time.
Overall, creating a digital twin is a complex process that requires a deep understanding of the physical asset or system, as well as expertise in data collection, 3D modeling, simulation, and integration. However, the insights provided by digital twins can be invaluable in improving the performance and efficiency of physical assets and systems, and can help to drive innovation and growth in a wide range of industries.